This project focuses on creating materials consisting of at least four elements through magnetron sputtering. We are interested in understanding how mechanical properties like strength and ductility vary with changes to compositions and expanding the material space for structural applications.
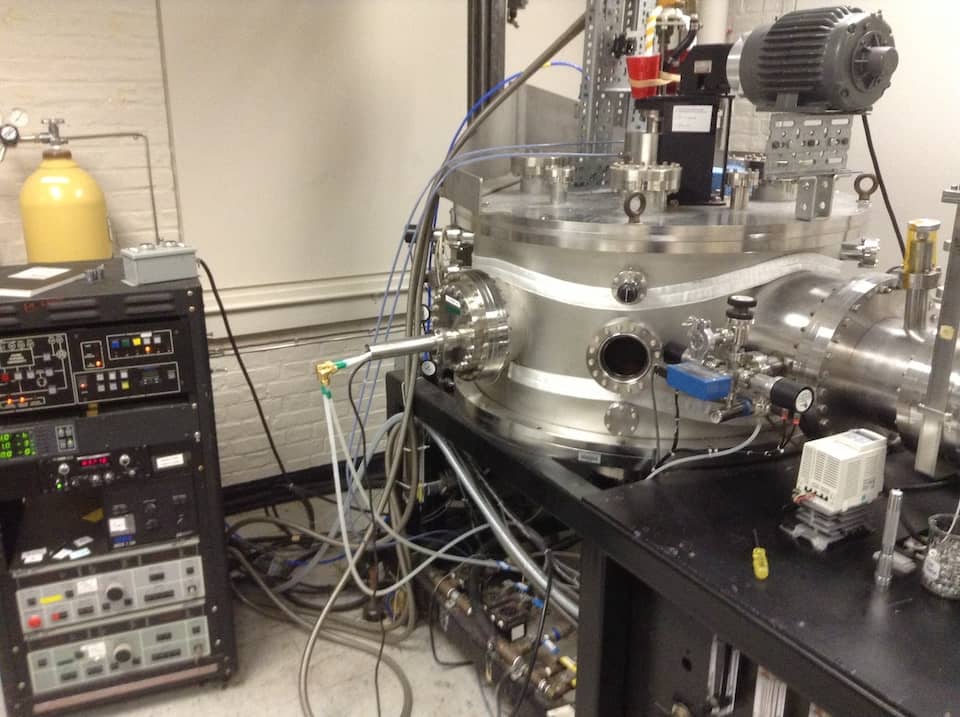
The development of structural alloys with revolutionary properties can be accelerated dramatically by screening large data sets collected from broad ranges of chemistries and microstructures. However, generating these data sets is daunting as conventional synthesis, processing, and characterization are extremely time-consuming. Here we will demonstrate the ability to use combinatorial studies that leverage fabrication and thermomechanical processing to produce samples with bulk-like microstructures and novel characterizations guided by machine learning/uncertainty quantification (ML/UQ) to rapidly generate large databases of sample chemistry, processing parameters, microstructures, and properties for bulk structural alloys.
Fabrication of samples relies on applying novel approaches to thick-film deposition using composite-material graded sputter targets and adaptation of a traditional sputter system for large-scale combinatorial depositions of multi-component alloys. This will form the basis of our three-tiered combinatorial approach and rapid characterizations guided by ML/UQ. The first two tiers use sputter deposition of thick, free-standing foils; the third uses directed energy deposition (DED) of bulk samples. All three tiers include thermomechanical processing to yield bulk-like microstructures guided by ML/UQ-assisted characterizations to rapidly screen properties and behavior.
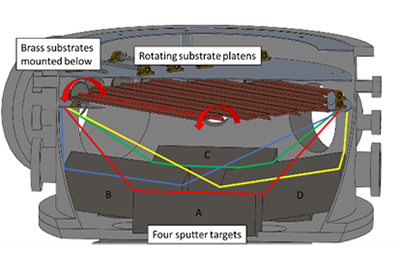
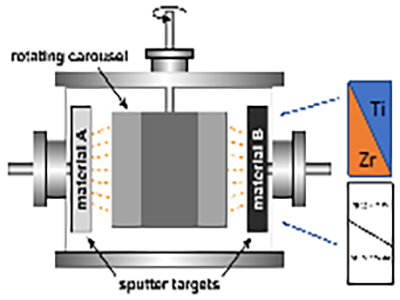
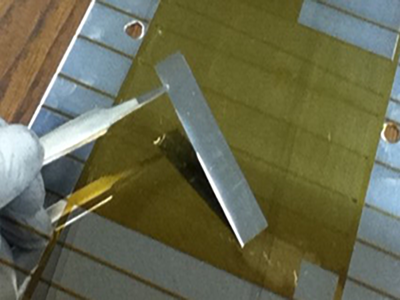
Fig 2. (a) Classical combinatorial setup with sputtering upwards onto stationary substrates; (b) hybrid combinatorial setup with sputtering horizontally onto rotating substrates; and (c) examples of thick foils being removed from polished and patterned brass substrates for testing at JHU
There is an extensive history of combinatorial thin film studies that generate material property data rapidly for a broad range of chemistries, allowing materials to be screened for potentially useful properties. To date, however, such studies have focused almost exclusively on materials’ functional properties (electrical, optical, magnetic, and thermal). This focus results, at least in part, from the use of thin-film deposition to produce sample libraries which necessarily are limited in both thickness and the variety of crystallographic textures produced. This is a serious problem for screening structural materials where the important mechanisms of deformation and failure (e.g., spall) are sensitive to microstructure on much longer length scales. It severely limits the applicability of traditional combinatorial approaches (based on thin-film deposition) to develop alloys for structural applications. Furthermore, techniques capable of producing bulk microstructures (including additive manufacturing) are often not well-suited to rapid screening of a wide range of alloy compositions.