Optimizing material properties by iterating through a series of experiments – fabricate, characterize, and repeat – can be time-consuming and expensive. Here we develop novel structural materials in a far more rapid and efficient manner using topological optimization methods to predict ideal material architectures and novel textile processing to fabricate those architectures. Unlike foams, tubes, or truss architectures which are commonly used porous structures, we believe 3D weaving can produce architectures with superior permeability, specific stiffness, heat transfer, damping, and other properties.
Compared to foams, tubes, or truss architectures, which are common porous structures, we believe 3D weaves offer superior properties such as permeability, specific stiffness, heat transfer, damping, and bioactivity.
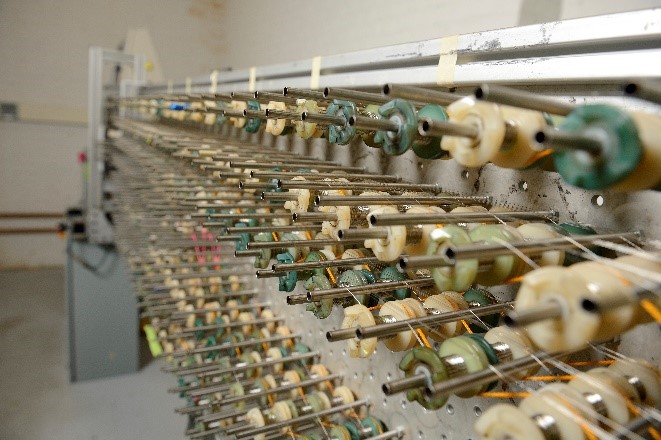
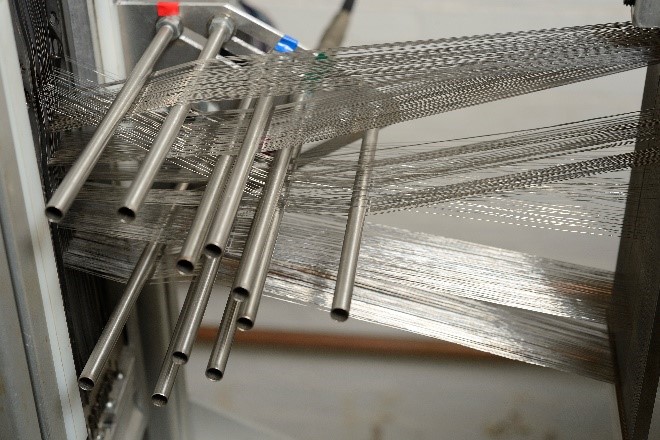
3D weave coated with hydroxyapatite
In this study, we demonstrated that a uniform coating of hydroxyapatite (HAp, Ca10(PO4)6(OH)2) can be electrochemically deposited onto bioinert metallic 3D woven bone scaffolds to enhance their bioactivity. The optimized HAp coatings are relatively uniform in thickness throughout the interior of the porous SS weaves and contain sub-micron scale HAp crystals. The finely structured coatings improve the bioactivity of the scaffold in short-term cell interaction studies.
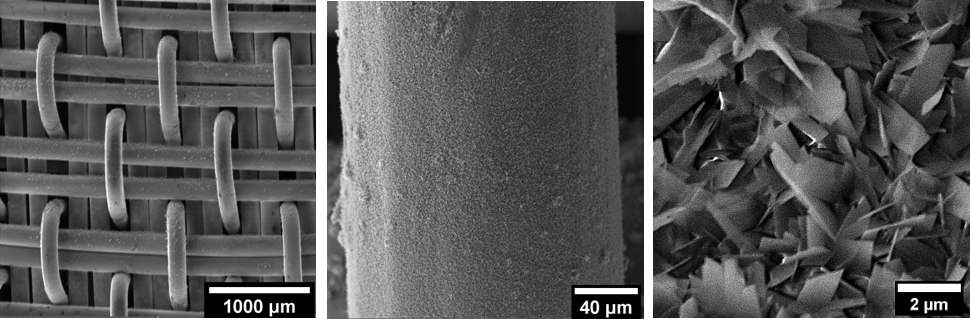
3D weave with exceptional damping properties
Complex mechanical systems such as satellites, airplanes, and automobiles can generate severe dynamic environments that require materials with elevated and optimized damping properties, elastic moduli, and service temperatures. In this study, woven lattices were first fabricated with different parent wires (stainless steel (SS), Cu, SS-Cu composite, NiCr). Then the surface Cu wires of SS-Cu weaves were selectively bonded with Cusil® to form more rigid, 3D woven structures. We demonstrate an ability to both tune and enable exceptional damping and moderate stiffness in metallic materials.
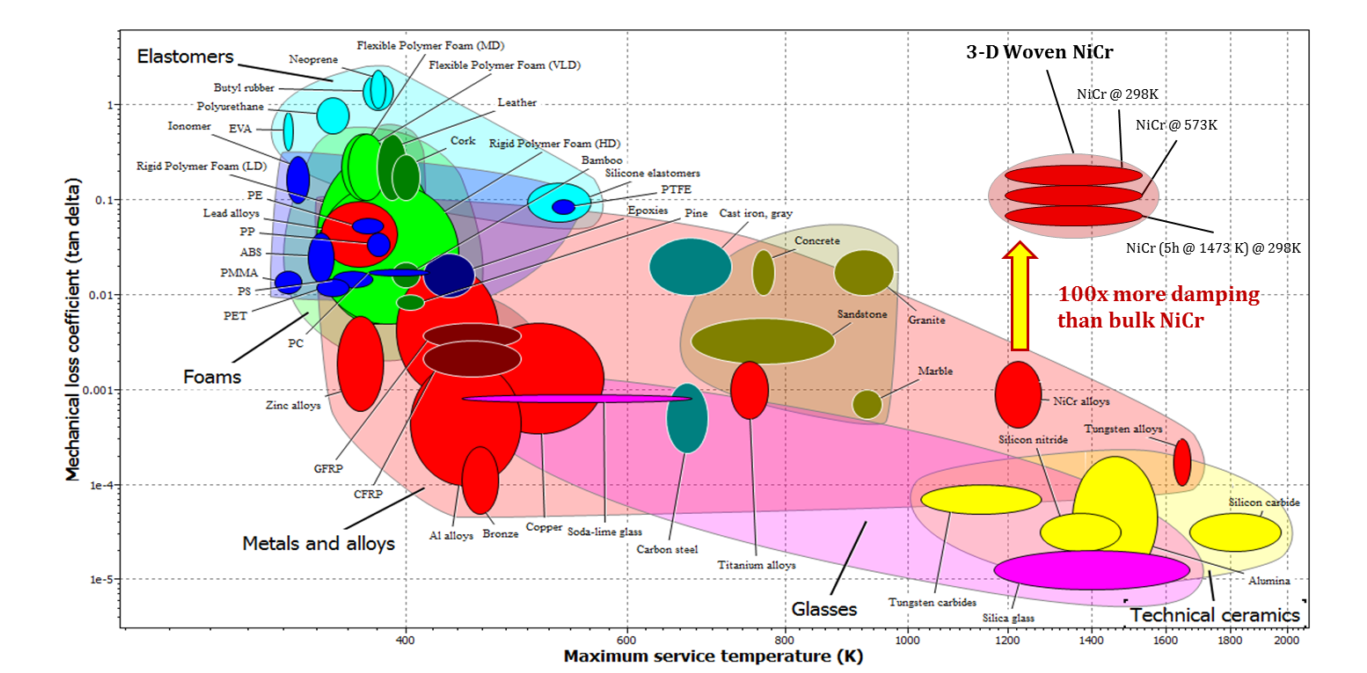
3D weave for heat transfer application
In this study, the heat transfer properties of 3D weaves were investigated using various distributive flow patterns. The corresponding heat transfer coefficients, surface temperature distributions, and pressure drops are quantified. Both fluidic and thermal properties were reported and compared to other common porous materials such as foams, fins, and truss architectures.
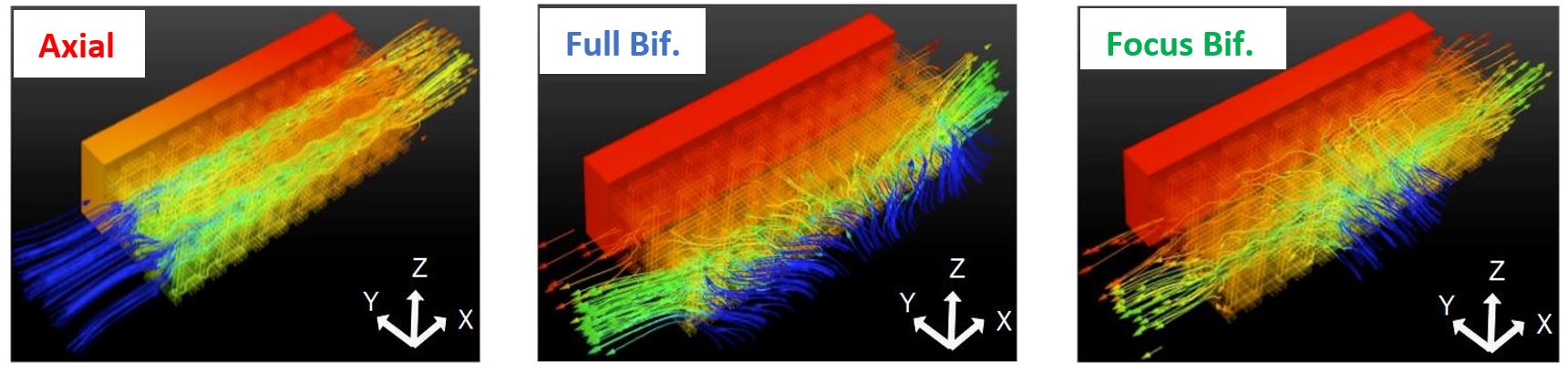
References
J. Xue, A. Farris, Y. Wang, W. Yeh, C. Romany, J.K. Guest, W.L. Grayson, A.S. Hall, T.P. Weihs, Electrodeposition of Hydroxyapatite on a Metallic 3D-Woven Bioscaffold, Coatings. 10 (2020) 715.
S.M. Ryan, S. Szyniszewski, S. Ha, R. Xiao, T.D. Nguyen, K.W. Sharp, T.P. Weihs, J.K. Guest, K.J. Hemker, Damping behavior of 3D woven metallic lattice materials, Scr. Mater. 106 (2015) 1-4.
L. Zhao, S.M. Ryan, S. Lin, J. Xue, S. Ha, T. Igusa, K.W. Sharp, J.K. Guest, K.J. Hemker, T.P. Weihs, Combining a distributed flow manifold and 3D woven metallic lattices to enhance fluidic and thermal properties for heat transfer applications, Int. J. Heat Mass Transf. 108 (2017) 2169-2180.